- Company
- Business Model
E-Trade
E-Projects
E-Services
E-Products
- Partners
- Sectors
- Media Center
- Contact
- Careers
Sustainability & Innovation
Maerz
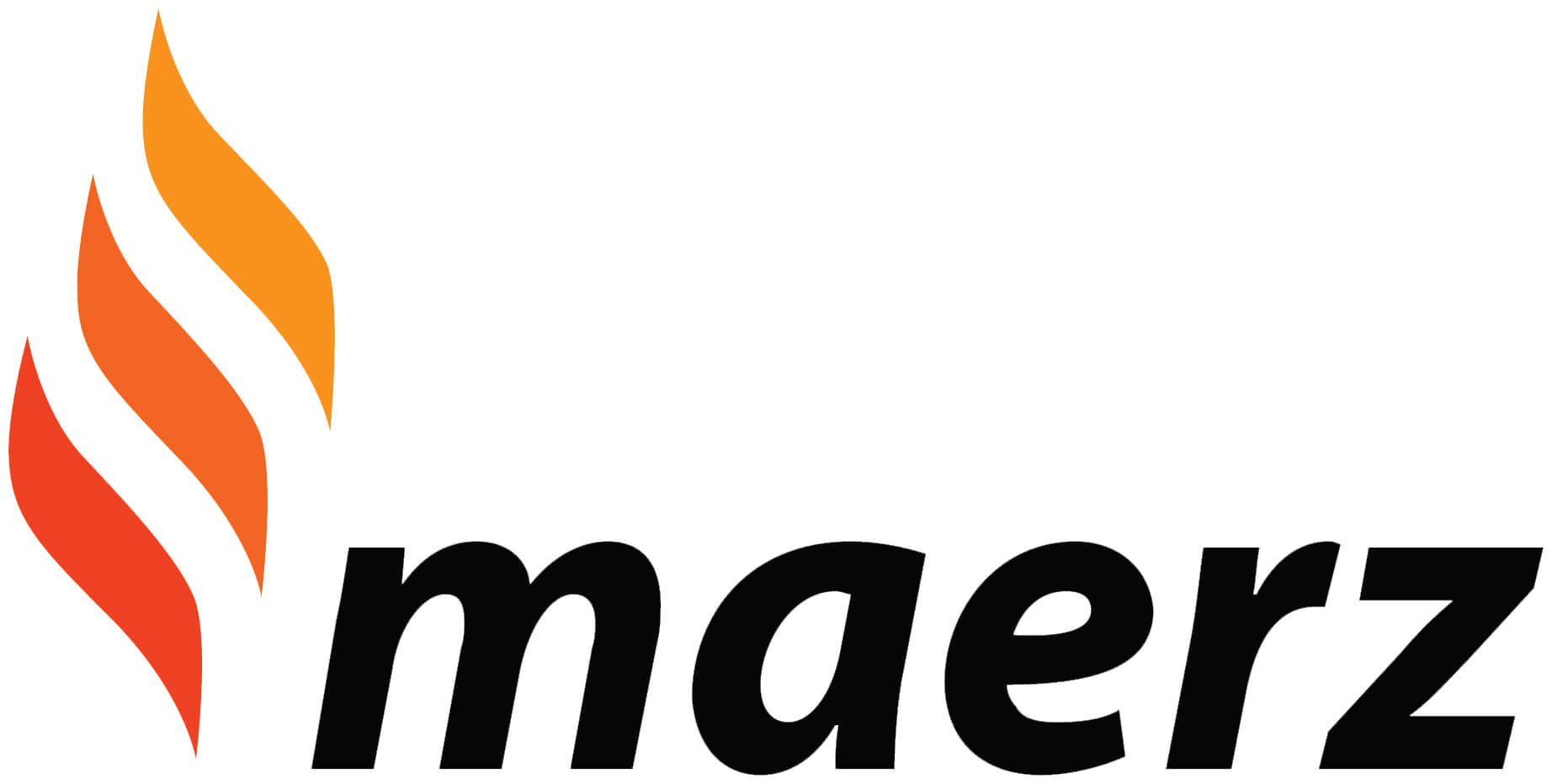
Maerz Ofenbau AG was founded in Zurich as early as 1950. Initially active in the steel industry, kilns for the lime industry soon became the core business.
EAST has been partnering with Maerz since 2021, Our both dedicated team that focuses on the planning, development and construction of kilns and hydration plants for the lime industry. We support our customers worldwide in the construction of new lime plants as well as in the modernisation of older plants.
From the first layout design, detailed engineering and professional project management, to the commissioning of the plant, you work with our highly qualified staff.
Our service team will advise you on all questions concerning the process, operation of the plants, possible measures to increase efficiency or the supply of spare parts.
Maerz PFR kiln
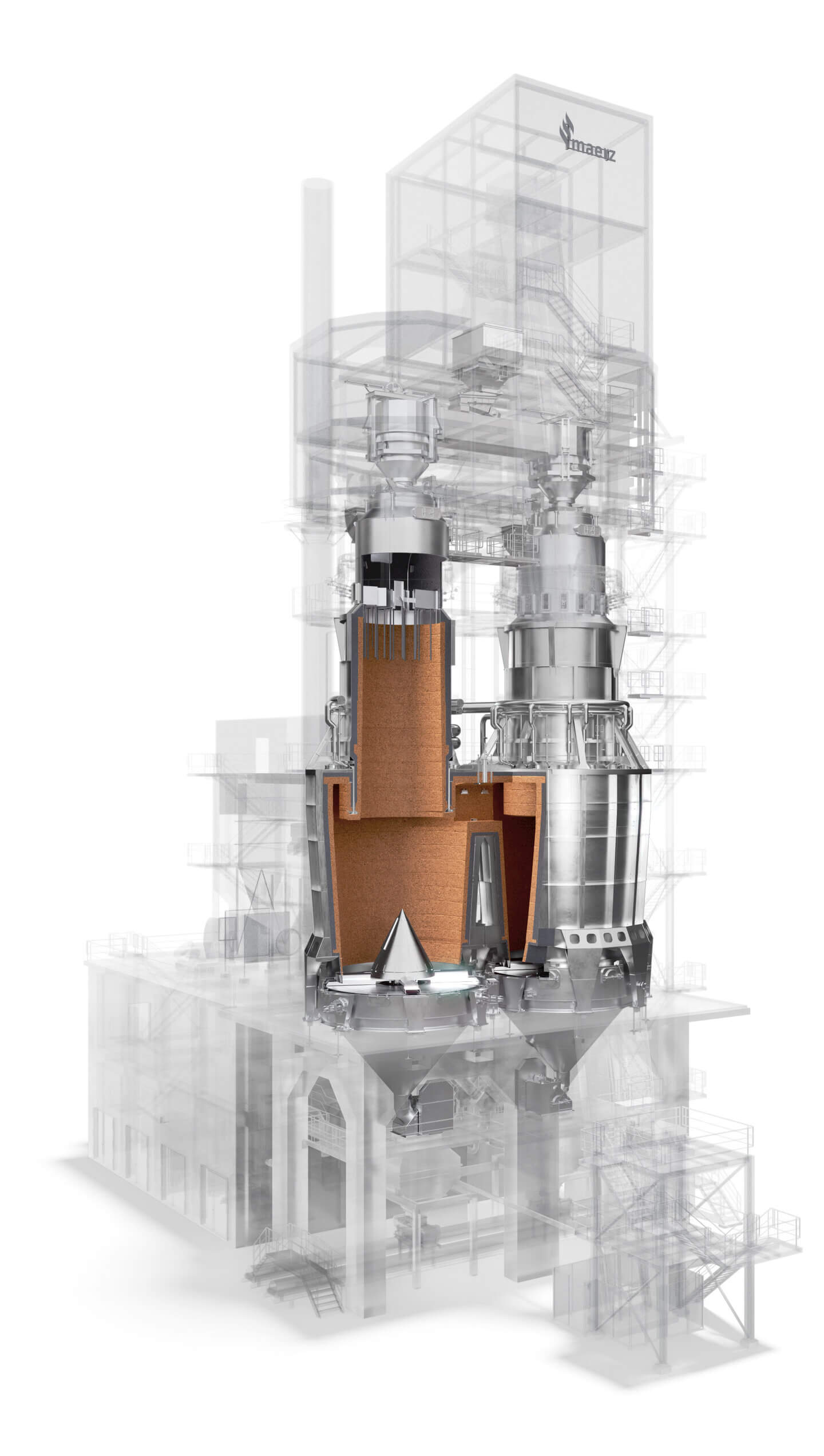
Maerz C series
Maerz C series is the further development of our classic circular kilns, which are used for production capacities of 300 to 800 tpd: a ring channel ensures that even with large shaft cross-sections, the fuel gases can flow into this ring channel evenly distributed over the circumference of the inner cylinder. This ensures a uniform heat distribution over the kiln cross-section and guarantees a high quality of quicklime.
The kiln’s charging system has been further optimised and, thanks to an intelligent distribution system, allows the simultaneous use of several grain sizes in order to optimise the utilisation of the quarry.
The layout of this new series of kilns is modular, so that the addition of further fuels is possible without any problems and without significant adjustments to the existing installation.
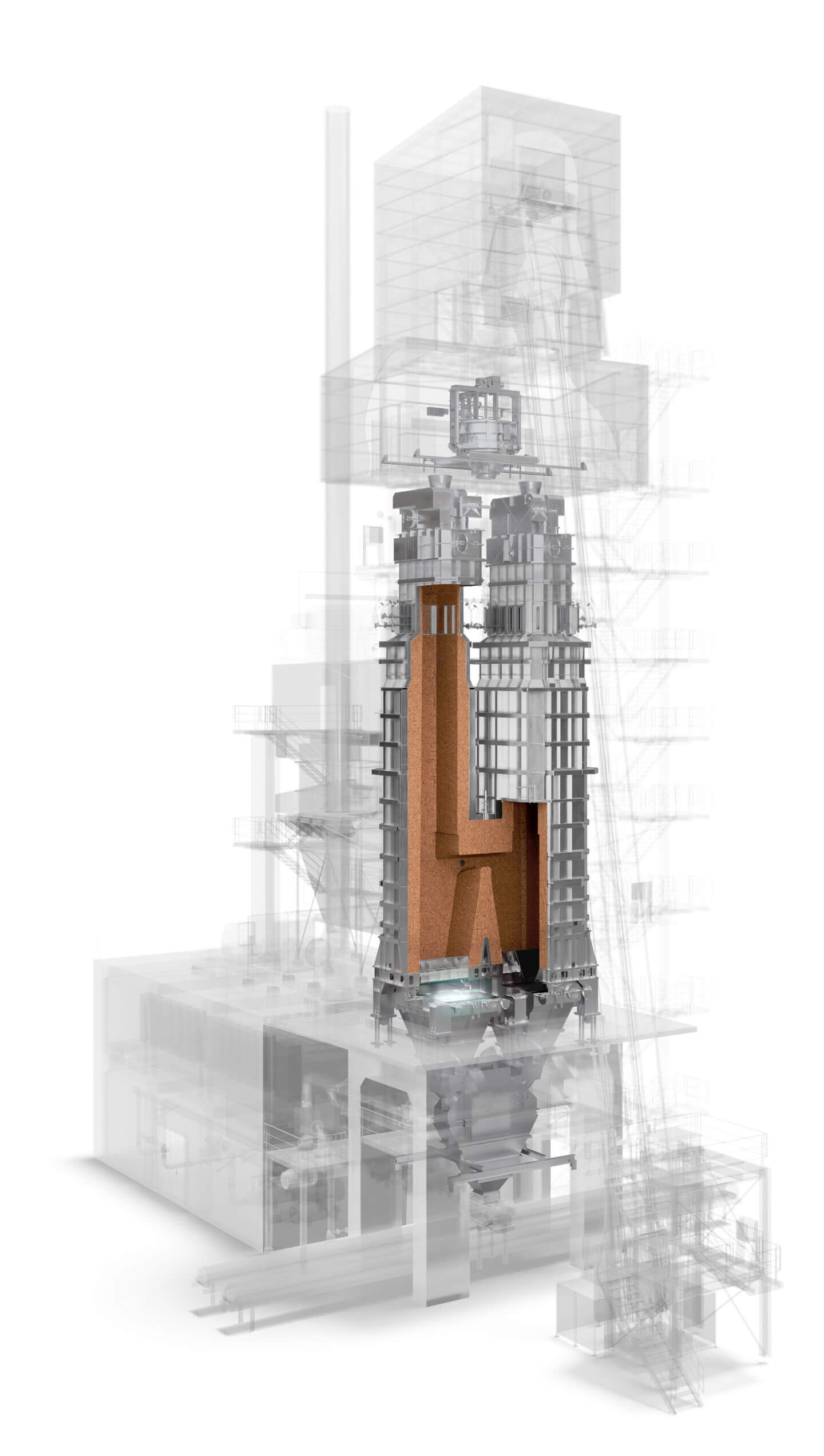
Maerz E series
Maerz E series is designed for production rates between 100 and 400 tpd. Their geometry with the direct cross-over channel between the two shafts, requires less steel and refractory material than circular kilns and has been optimised with respect to investment costs.
In these kilns, too, not only can the quality of the quicklime be optimised by means of a special charging process, but – as in the circular kiln – several grain sizes can optionally be used at the same time.
In the E kiln, it is also possible to burn the lime harder by installing additional side burners under the cross-over channel, thus significantly lowering its reactivity. We call this kiln a “”hybrid kiln”” – it gives you the flexibility to produce different types of quicklime with just one kiln.
Maerz HPS kiln
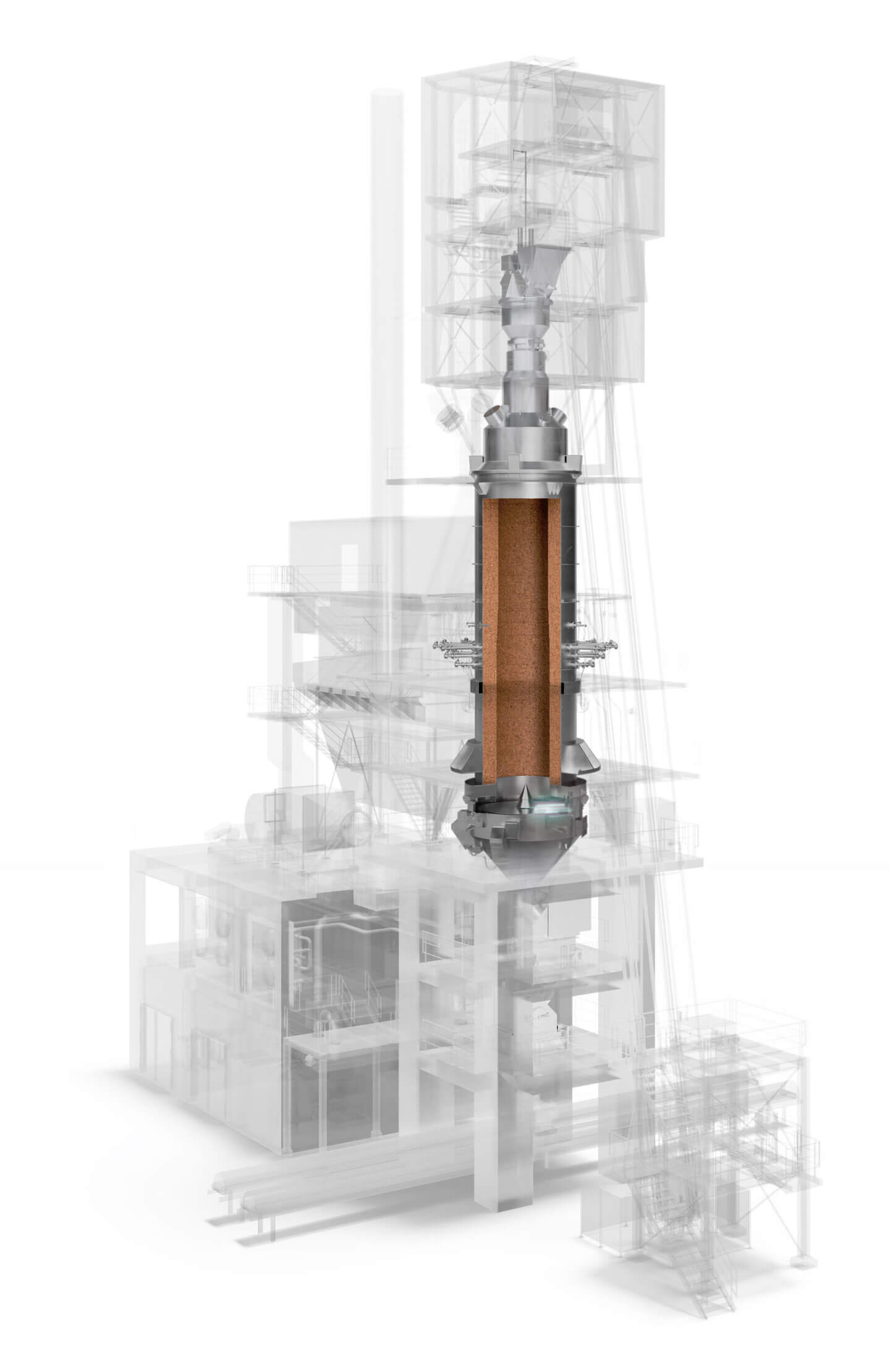
For some applications in the lime industry, a quicklime with medium or low reactivity is required. In these cases, smaller kiln capacities are often sufficient. This is precisely why it has been developed the Maerz HPS kiln (High Performance Shaft Kiln) for production rates of 100, 150 and 200 tpd: a compact single-shaft kiln that operates on the counterflow principle and into which the fuel is fed at the lower end of the burning zone via radially displaceable burner lances. These extend far into the material bed and thus ensure that the heat is optimally distributed over the entire shaft cross-section.
If the HPS kilns are designed in a special way, their continuous off-gas flow can also be enriched, without oxyfuel firing, to a CO2 content that enables their use, for example, in the sugar industry.
Maerz EcoKilns
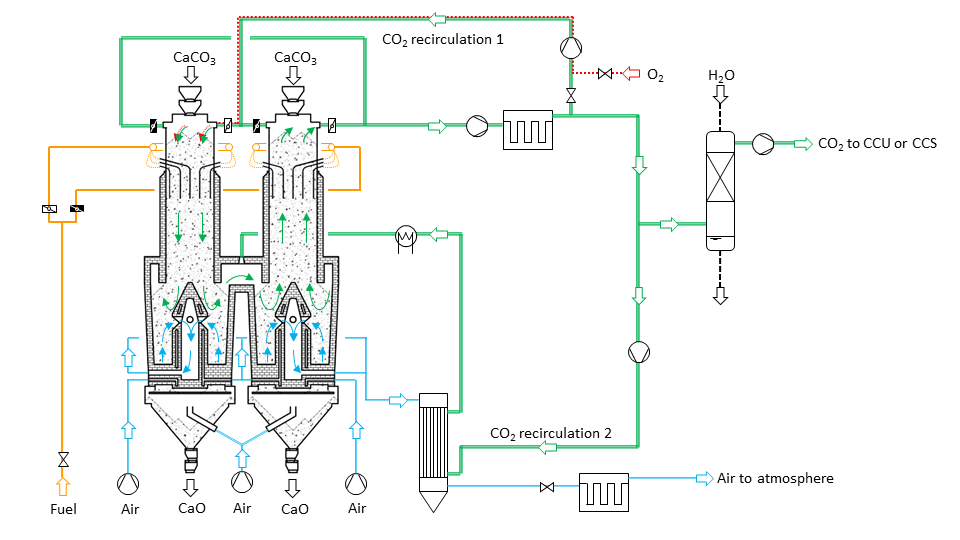
To date, when dealing with lime kilns, there was always consideration about optimising the process for the production of quicklime. The CO2 emissions from the kilns were not taken into account.
This has changed fundamentally with the climate debate: innovatively and with a lot of passion, Maerz has worked step by step to enrich the CO2 in the kiln off-gas as high as possible. In the process, Maerz filed patents for many inventions and finally developed the Maerz EcoKiln series. The highly concentrated CO2 can thus be liquefied easily and fed into a further use or sequestration.
The Maerz EcoKiln series can be expanded in several stages: in the simplest variant, only the combustion air can be replaced by the oxygen-enriched kiln gas (oxyfuel operation). This allows CO2 contents in the kiln off-gas of 40 – 45 % to be achieved. This configuration is ideal for use in the soda and sugar industries, where in many cases replacement investments for old mixed-fired kilns are due in the next few years.
Maerz hybrid kilns
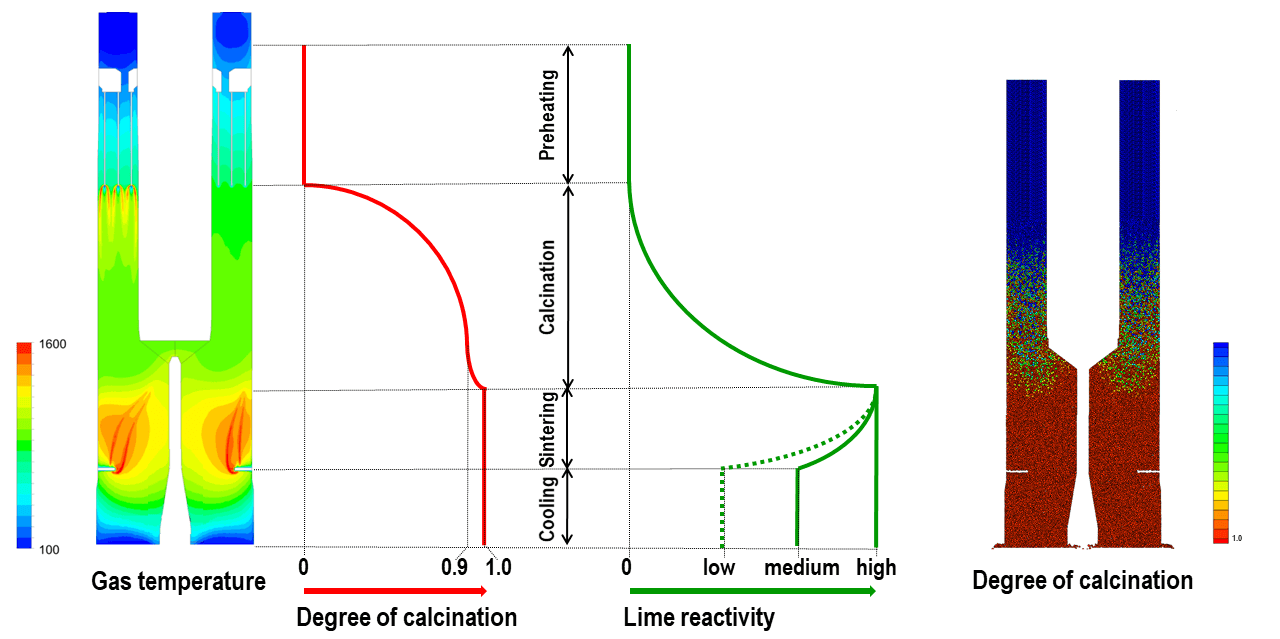
Flexibility with respect to product quality and fuel use is written in capital letters in lime plants today. In addition to highly reactive lime in large quantities, medium-reactive lime in smaller quantities is also needed for special applications. That is no problem with Maerz hybrid kiln, It can be operated like a normal PFR kiln and, If necessary, the lime can be thermally posttreated by switching on side burners in the lower kiln area, Thus setting the desired reactivity.
Maerz Finelime kilns
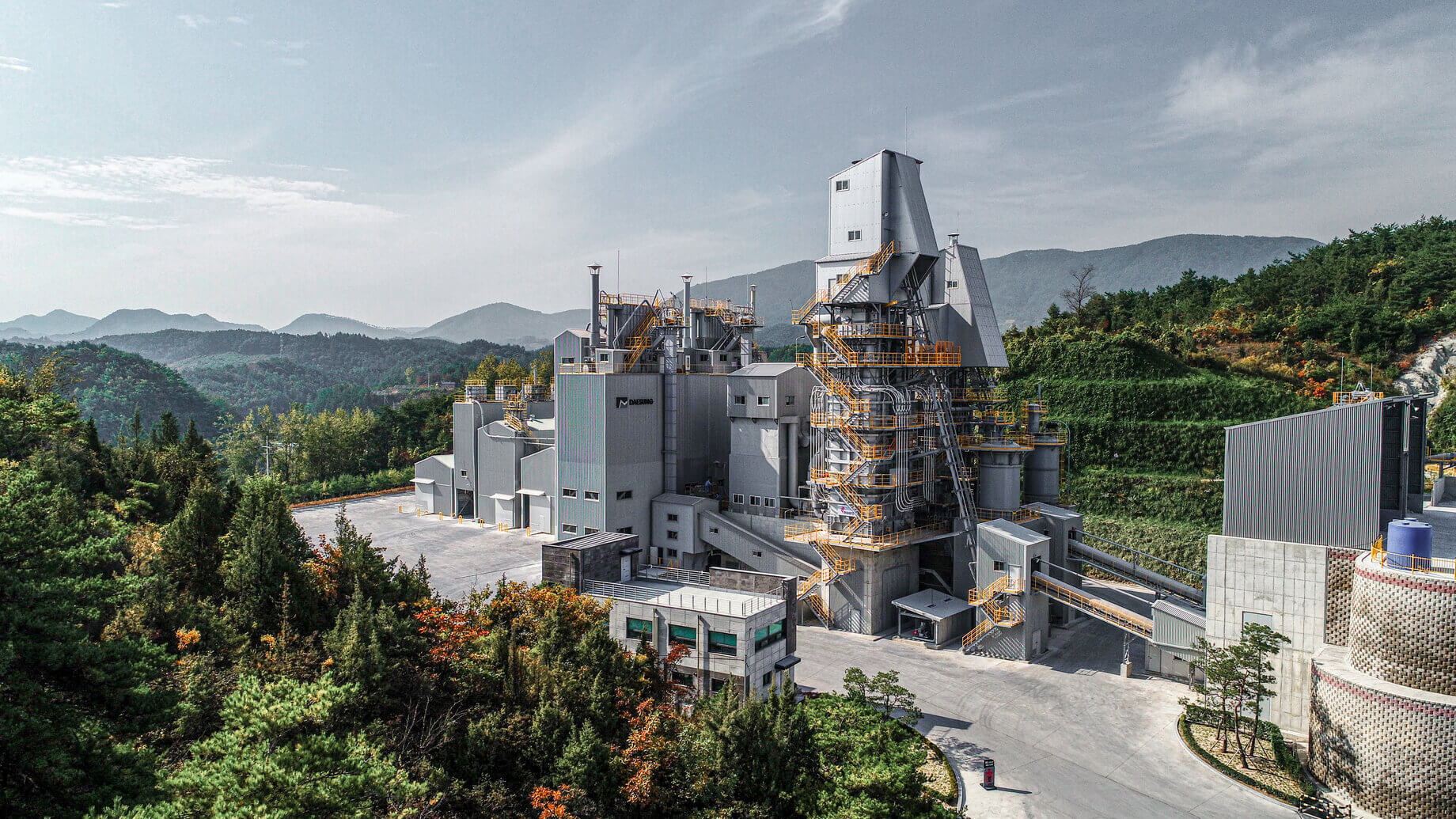
Maerz PFR kilns can also be designed in a special way that allows small stones to be fired in a shaft kiln, Thus increasing the degree of utilisation of the quarry. Both the geometry of the cooling zone and the preheating zone are optimised for the use of small stone, so that this design of Maerz Finelime kilns can only be chosen for new kiln construction.
Another modification enables the simultaneous use of several grain bands for kiln operation, each of which is fed into the kiln according to an optimised pattern. This allows the total bandwidth of grain bands to be significantly expanded, which in turn optimises the utilisation rate of the quarry. This upgrade can also be carried out on existing plants, provided there is sufficient space for several stone bunkers in the area in front of the skip.
Maerz external cooler
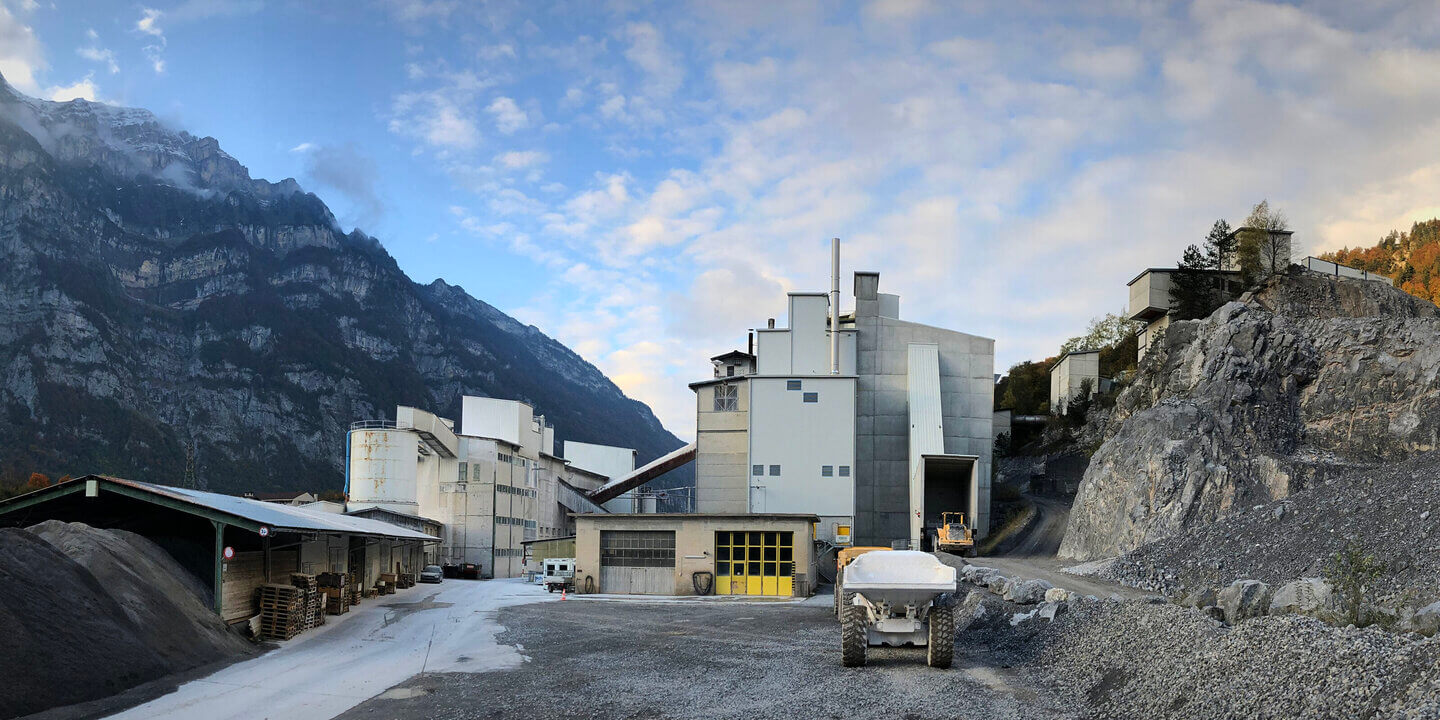
Maerz has developed a patented process to further optimise the cooling process in kilns with a direct overflow channel. This makes it possible to produce quicklime of the highest quality, as used in the food industry, for example. At the same time, the residual CO2 content can be kept very low and the reactivity very high.
The quicklime is cooled in two steps: a reduced supply of cooling air into the shafts keeps the temperature of the quicklime in the upper part of the cooling zone at a constantly high level. In this process, the lime is discharged at higher temperatures compared to conventional lime kilns. Further cooling of the quicklime takes place in a second step in an external cooler, which is installed under the discharge flaps of the shafts. Depending on the space available, an external cooler can also be installed in existing plants.
High-pressure fans
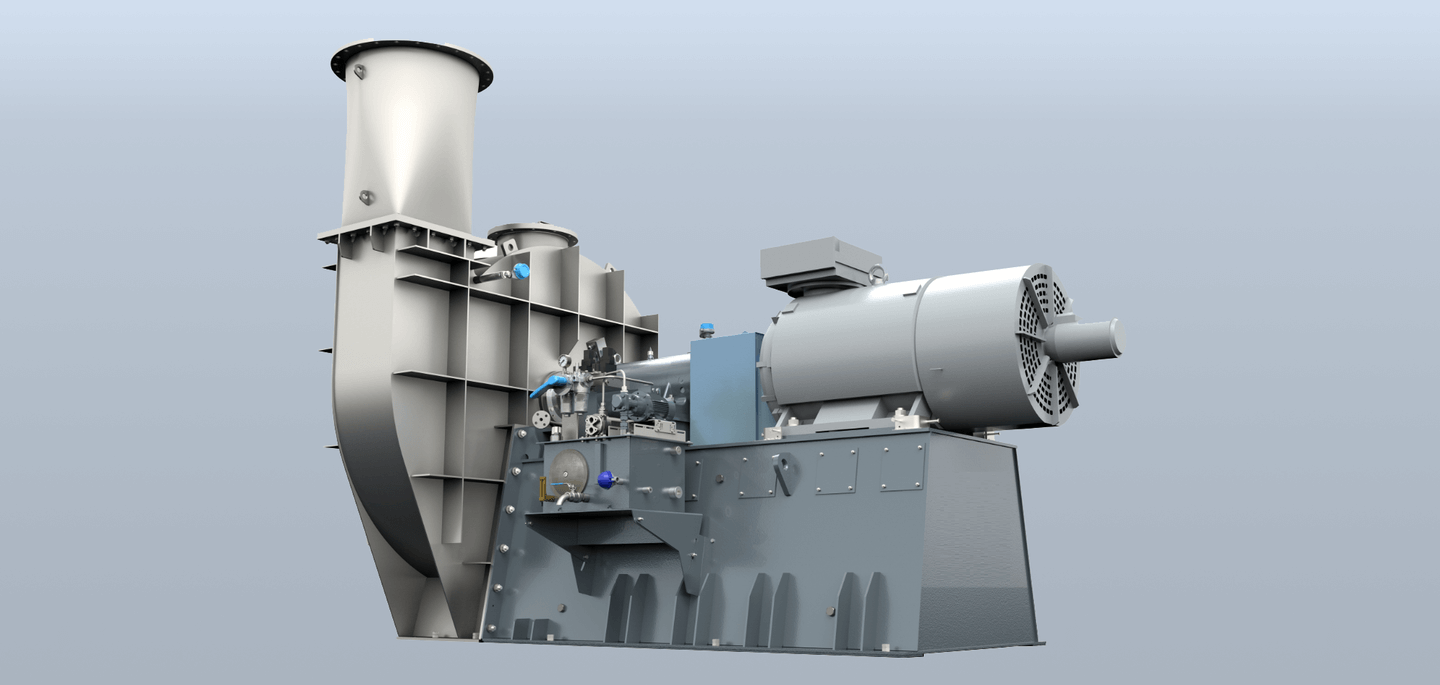
Maerz kilns operate at positive pressure with the required process air for combustion air, cooling air and, in the case of a PFR kiln, lance cooling air usually being compressed using rotary piston blowers.
With a new generation of high-pressure fans, the required air volumes (or also the recirculation gases in oxyfuel operation) and pressures can be provided with up to 25 % lower electrical power consumption. This can bring significant savings, especially with larger kilns, so that a conversion pays for itself after a relatively short time, even on existing systems.